Ensuring Consumer Safety and Operational Efficiency in the Food and Beverage Industry
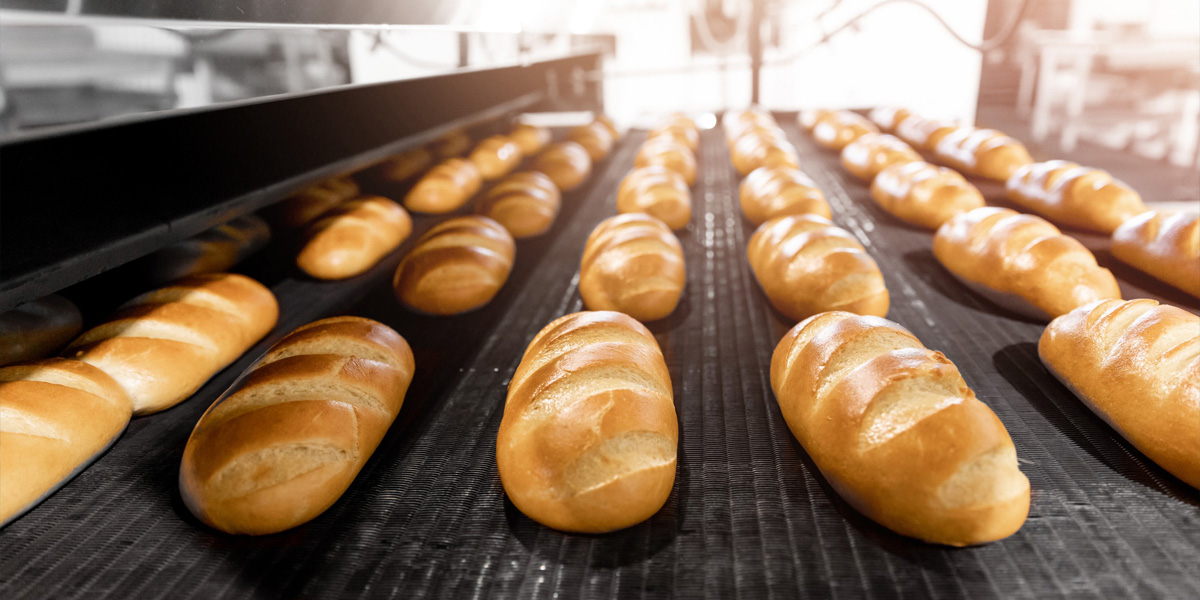
Compressed air is used in almost every production process in the food and beverage industry. Undetected leaks can lead to serious consequences, such as contamination of products, reduced efficiency, increased downtime, and safety risks, which makes using effective predictive maintenance methods and tools absolutely critical.
Industry-typical applications for compressed air include moving products, operating pneumatic tools, and pumping liquids for a variety of purposes in production chains, packaging, and cleaning, with multiple compressor assets connecting through pipes to deliver this vital compressed air. This is why compressed air leaks can cause such significant problems for food and beverage manufacturers, as they not only lead to high energy costs but also jeopardize manufacturing efficiency, product quality, and the safety of food and beverage products.
Effective predictive maintenance inspections of compressed air systems are essential for ensuring the quality and safety of food and beverage products.
Industry-Specific Challenges From Costs to Contamination
The food and beverage industry is heavily regulated to ensure public safety and protect consumers from potential health hazards. This also means that air leaks cause certain industry-specific challenges. Firstly, vacuum leaks can contaminate the food and beverage products, as the air in a manufacturing facility can contain particles and contaminants that can be harmful to food and beverage products. Vacuum leaks can introduce these contaminants into the products, leading to spoilage, quality issues, and even health risks for consumers.
Secondly, compressed air leaks can reduce efficiency and increase operating costs. Compressed air systems are energy-intensive and require significant amounts of electricity to operate. When there are leaks in the system, the compressed air pressure drops and the system has to work harder to maintain the required pressure, resulting in increased energy consumption and higher operating costs. As 24/7 operations are not uncommon in the food and beverage industry, these additional costs can quickly accumulate into significant amounts.
And finally, compressed air leaks can affect the performance of pneumatic tools and equipment, reducing their effectiveness and leading to downtime for repairs and maintenance.
FLIR Si124 Acoustic Imaging Camera
An Acoustic Solution That Meets the Needs
To avoid problems like impaired product quality, increased operating costs and consumer safety risks, food and beverage manufacturers need to regularly inspect compressed air systems to ensure that they are functioning correctly and free from leaks. Using an acoustic camera such as the FLIR Si124-LD Plus helps identify even very small leaks promptly, improving the system’s efficiency, reducing operating costs, and ensuring the quality and safety of food and beverage products. An acoustic camera also allows for accurate leak detection from a long distance even in a noisy environment typical for the industry, without having to halt operations. Further benefits include the AI-driven automated distance, leak size and cost estimates, which greatly facilitate predictive maintenance decision-making in the food and beverage industry.
Benefits of an Acoustic Camera for Air Leak Detection in the Food and Beverage Industry
- Saves time, energy and costs by locating hidden compressed air leaks in time.
- Increases operational efficiency by preventing unplanned downtime through early detection of air and gas leaks.
- Scans large areas quickly and pinpoints critical problems accurately, even from a distance and in noisy environments.
- Ensures product quality and compliance to the regulation and controls the production facilities and equipment are subject to.
- Requires minimal training and is easy to incorporate into the maintenance cycle.
- Allows for inspections to be carried out without halting operations.
- Provides real-time results and actionable data for maintenance and repair plans through machine-learning-driven analytics.
FLIR Thermal Studio Suite with the Si-Series Plugin
For more information about thermal imaging cameras or about this application please visit: www.FLIR.com/si124