7 Things to Look for in an Acoustic Imaging System
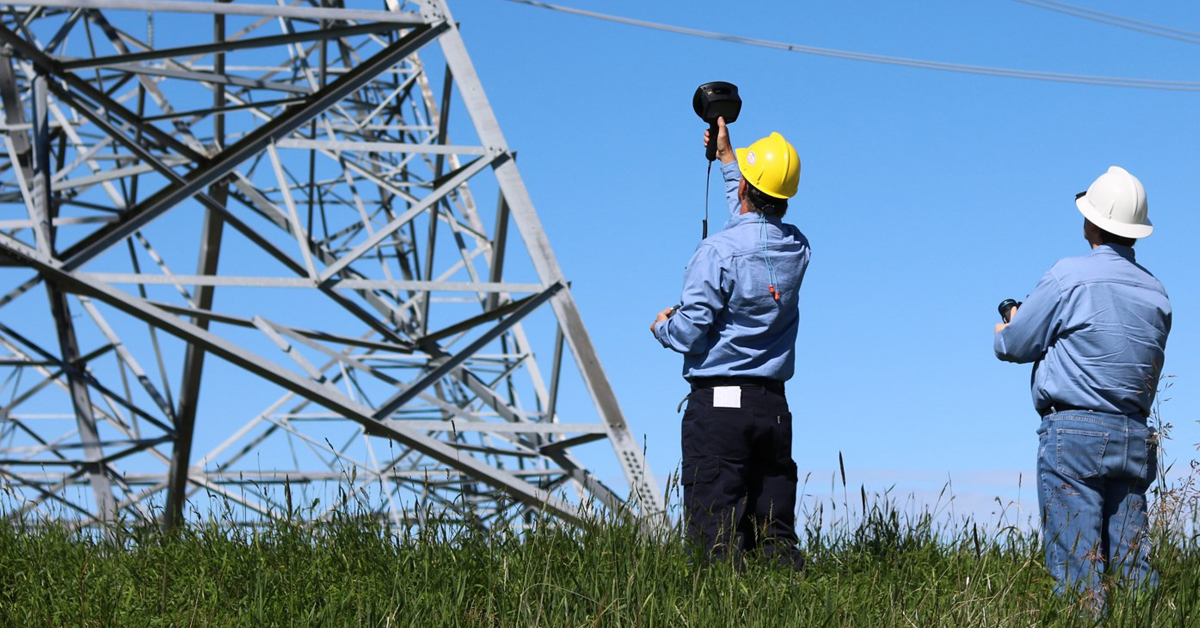
Compressed air leaks, vacuum system leaks, electrical partial discharge—these are all expensive system issues that lead to unplanned outages, productivity reduction, consume power and may negatively impact worker safety. Ultrasound imaging with an acoustic camera is an easy-to-use, effective way to detect these equipment issues as part of a complete asset management plan. Acoustic imaging typically allows professionals to complete their inspections 10 times faster than with traditional methods.
So what should you look for when selecting an acoustic imaging camera? Here are seven things to consider before making your purchasing decision.
1. One-HANDED OPERATION
For safe operation of any handheld tool, it is imperative that scanning must be performed using one hand so that the other hand may be used to hold on to railings or be available to adjust safety equipment like hardhats or glasses. A free hand also ensures easy documentation via touchscreen to ensure accurate identification of targets and speedy reporting.
2. Decision Support
Quantification of compressed air leaks, including estimated leak cost, helps maintenance departments prioritize repairs and makes it easy for maintenance managers to point to the impact their team is having on a company’s bottom line.
Partial discharge issues can be difficult for new inspectors to diagnose with traditional techniques, leading to uncertainty or lack of action on corrective action. Acoustic imagers that not only locate partial discharge issues, but also classify as to type, assess the issue severity, and provide a clear course of corrective action remove that uncertainty and enable maintenance managers to make quick, effective decisions to reduce maintenance costs or even avoid catastrophic equipment failure.
3. Suitable Software
Software needs vary. Some users prefer as much as possible to be built into the tool, while others want analysis and reporting to be simple, without cost, and without computer installation. Still more need on-premises software that does not connect to any 3rd party cloud service provider due to restrictive IT policies.
Another factor may be the desire to combine your ultrasonic imaging and thermography inspection into one software package, one report, or perhaps even on the same page so you can directly compare an issue using two different inspection modalities.
Whatever your situation, it is important to choose a system that meets the right requirement for your business and is capable of growing with you as your predictive maintenance program matures. The FLIR Si124 makes all these options available.
4. NUMBER OF MICROPHONES – MORE IS BETTER
In the pursuit of quieter noises, more is better. Acoustic imaging cameras may employ dozens of microelectromechanical system (MEMS) microphones to collect and characterize sound. While MEMS are small, use little power, and are very stable, they also generate their own noise that interferes with an individual microphone's ability to pick up very quiet sounds. The solution for best performance is to increase the number of microphones in use; simply doubling the number of microphones improves the signal-to-noise ratio enough to remove three decibels of unwanted sounds.
Consider this example. One microphone might create enough self-noise to make it impossible for the system to pick up a compressed air leak generating a 16.5 kHz signal.
An acoustic camera with 32 microphones would be able to detect that leak, but the signal-to-noise ratio is still too poor to hear anything quieter.
In contrast, a camera with 124 microphones can pick up both the 16.5 kHz leak and one that is 18.5 kHz, making it easy to detect, locate, and quantify the small leak.
5. OPTIMAL FREQUENCY RANGE
One of the first features you will see listed on an acoustic camera datasheet is the camera's frequency range. You might think that you need the widest range possible in order to pick up the widest range of sounds. In reality, the most effective frequency range for detecting ultrasound waves created by compressed air leaks or partial discharge is between 20 and 30 kHz, for several reasons.
For compressed air or gas leaks, 20 to 30 kHz range aids in distinguishing leaks from the background noise in a factory. The amplitude of machinery noise usually peaks below 10 kHz and trends down to zero at 60 kHz, whereas most leaks peak between 20 and 30 kHz. Since there is a greater difference between the leak noise and the background noise between 20-30 khz, compared with higher frequencies, it's easier to detect the air leak in this frequency range.
Both the compressed air and machinery noise follow the same downward amplitude trend in the 30 to 60 kHz frequency range, making it difficult to distinguish between them. Therefore, working within the 20 to 30 kHz range is more effective.
For users looking for leaks or partial discharge from a distance, the 10 to 30 kHz range is again optimal. This is because higher frequency waves get absorbed by the air and thus travel shorter distances. In order to detect leaks at a long distance, or partial discharge from high voltage equipment in an outdoor setting, your camera needs to be attuned to lower frequency, farther-traveling sounds.
Higher frequency sounds, up to 65 kHz, are ideal for detection of issues that can be inspected at close distances, like some compressed air, compressed gas, or vacuum leaks. Your acoustic camera should be able to adjust to use the most appropriate frequency spectrum for the task being performed.
Curves showing relative sound volume change with distance for different ultrasonic frequencies
6. INTELLIGENT ANALYTICS
Legacy ultrasound technology detects issues through frequency tuning, but there is another, more effective technology that makes use of the advances that have recently taken place in computing power and machine learning. The FLIR Si124 utilizes machine learning to distinguish the characteristics of sound other than frequency in much the same way you can distinguish between the sounds created by two different musical instruments playing the same note (ie, frequency). For the Si124 it is easy to distinguish between an air leak and background machine noise because those two sources sound as different as a bell compared to a harmonica.
Furthermore, machine learning makes operation of the tool a great deal simpler for partial discharge analysis. Experts in ultrasound defect recognition have “tagged” the data, providing guidance on issue severity and appropriate corrective action. As a result, you get the benefit of their expert experience without undergoing days of training and hundreds of hours of practice. This is similar in many ways to the language translation apps on your smartphone which translate text for you without requiring you to spend years learning a new language.
7. -FIELD-REPLACEABLE BATTERY
Professional tool users always have a backup battery in the charger, just in case, because you never know when you will be called upon to troubleshoot a problem. Your acoustic imaging tool should be able to easily swap batteries in the field so you can charge and work at the same time.
Thanks for taking time to learn about acoustic imaging cameras. We hope you will contact FLIR to request a demonstration of this powerful, yet simple-to-use tool. Whether you intend to use it for leak location and quantification or partial discharge location and analysis we know you will be extremely impressed with the Si124.